Ethanol plants have discovered a way to transform distillers’ grain into a valuable by-product rich in protein and fiber. What was considered waste is now considered a highly nutritious and cost-effective animal feed. However, this transformation brings its own set of challenges. Although wet cake can be sold locally, its limited shelf life presents obstacles in transportation over long distances or extended storage periods.
This is where we step in to assist you with drying DDGS.
Drying DDGS opens a world of possibilities.
Crops like corn, rice, and wheat serve as crucial ingredients in alcoholic beverage production and are also fundamental to ethanol manufacturing. Because of their nutritious composition, both brewers’ spent grain and ethanol by-products are excellent for animal feed. However, the challenges associated with drying DDGS depend on the properties and origin of the feedstock and can be hard to tackle.
Challanges to face.
Variations in particle size can impact not only nutrient digestibility and palatability but also mixing efficiency, pellet quality, and bulk density. Consequently, manufacturers of feeds or feed supplements often prioritize the particle size and uniformity of feed ingredients. However, DDGS product streams are usually characterized by inconsistent particle sizes, posing challenges to uniform drying processes. This inconsistency can lead to difficulties achieving uniform drying, which is crucial for product quality. Additionally, traditional drying techniques for DDGS carry the risk of explosions due to the explosive nature of dust, particularly at high concentrations and temperatures. Moreover, even though drying distillers’ grain opens up a wide range of commercial opportunities, drying requires a lot of energy. With increasing environmental concerns, more companies take issue with the environmental consequences of such energy use and its environmental impact.
How can these issues be solved?
Swedish Exergy knows that DDGS drying is a sensitive process. You can damage the DDGS by adding foul taste by drying with an incorrect process at the wrong temperature with a longer residence time in the dryer. It can also cause burning and/or stripping the DDGS from valuable minerals and proteins that the animals need. Instead, a stable and optimized drying process can improve the product quality, shelf life and nutritious value of the DDGS.
Let us show you what we mean.
The superheated steam dryer for drying DDGS.
Our solution is a closed, pressurized system exposing the wet product to superheated steam. The steam serves as a medium to transport the product within the dryer. The heat from the heating medium is transferred to the steam and suspended product through the superheater surfaces, ensuring no contact between the heating medium and the steam or product suspended in the dryer. This design enables the utilization of various heat sources like flue gas, steam, thermal oil, or electricity for the dryer.
After passing through the loops, a cyclone separates the dried product from the superheated steam. The steam is recirculated while the dried product is discharged through a rotary valve. A portion of the dried product proceeds to the mixer, where it mixes with the wet product. The partially dry mixture is then fed back into the dryer.
The water in the wet product converts into steam during the drying process and is discharged through a pressure control valve to maintain constant pressure. The residence drying time ranges from 5 to 10 seconds. The Exergy Superheated Steam Dryer’s operating temperature and pressure are optimised to achieve ideal drying conditions, ensuring uniform drying throughout the product.
Optimal solutions.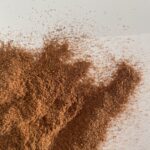
The DDGS produced when dried in the ExergyPSSD® has an increased value in bypass protein. It undergoes complete sterilization during drying and avoids oxidation due to the lack of air in the dryer. The oxygen-free environment in the dryer also eliminates the risk of fire or explosion. Since the dryer is a closed-loop system, there are no atmospheric emissions, eliminating the need for VOC or odor treatment. Moreover, the ExergyPSSD® is highly energy-efficient, recovering at least 80% of the energy input, resulting in a consumption of only 150 kWh/ton of water evaporation.
The Exergy Superheated Steam Dryer eliminates the current challenges the industry faces.